Reduced cleaning time = less downtime
A major issue for the foundry and forging industries is the downtime caused when cleaning permanent aluminium moulds, core box vents, semi-solid castings and die casting machines. Typical manual cleaning methods require cool down, disassembly, unproductive hours of messy hand cleaning or bead blast cleaning, and then reassembly. In addition, most traditional cleaning methods are not fully effective and often result in damage to the part or equipment.
Dry ice cleaning offers significant improvement in cleaning times (up to 60%) as well as reduction of damage to equipment and resulting scrap product. As dry ice blast cleaning allows a non-conductive, in-place method to clean parts, even touch-up cleanings are safe and easy.
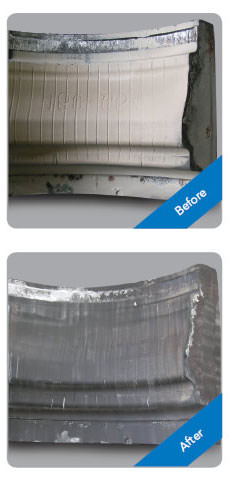
Applications
- Permanent aluminium moulds
- Refractory coatings
- Core boxes and vents
- Die cast tooling
- Shell core moulds
- Semi-solid castings / forging
- Remove resins and release agents
- General equipment & facility
- Conveyors
- General part cleaning
Key Benefits
- Reduce production downtime
- Eliminate disassembly of moulds
- Clean better, hot and in place
- Eliminate waste disposal cost
- Increase production time
- Non-abrasive, no damage to tooling
- Environmentally responsible
- Delivers superior as-cast finish
Tell us about your specific cleaning needs – contact us today